Suppression of Chatter in High-Speed Machining
RoMaDyC » Areas of Research » Dynamics and Control » Smart Machining
Machining chatter is a self-excited vibration occuring between the cutting tool and workpiece. Large amplitude vibrations caused by chatter may lead to damaging the cutting tool and/or the inability to hold part tolerance. It follows that the onset of chatter is a significant limiting factor in material removal rates when machining. To maximize the productivity of the machining process, chatter must be avoided through laborious tuning of the tool stiffness and spindle speed.
A spindle supported on active magnetic bearings (AMBs) has the opportunity to attenuate machining chatter through robust control of the AMBs. The robust control chatter-avoiding strategy includes a cutting force model in addition to the spindle model in controller design. The resulting controller stabilizes both the chatter and the instability inherent in the AMBs.
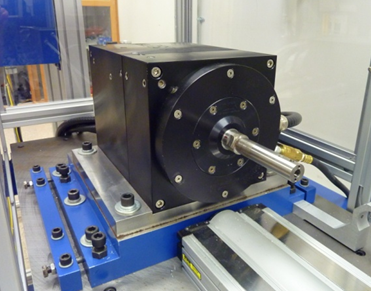
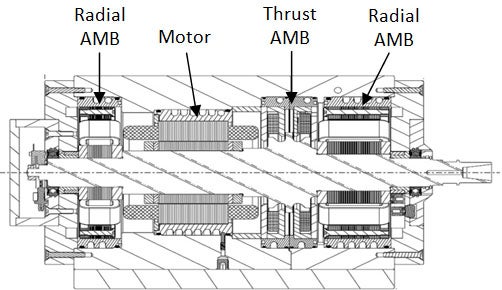
A high-speed AMB boring spindle at RoMaDyC serves as the platform for this research. The μ-synthesis technique has been used to design a robust MIMO controller for magnetic levitation and chatter prevention. Uncertainties are utilized in the cutting force model, maximizing the chatter-free region over the entire running speed of the spindle. The resulting controller is compared to a nominal robust controller designed without the cutting force model. A significant increase in the critical feed-rate before the onset of chatter is found, indicating that the chatter prevention controller enables faster feed rates.
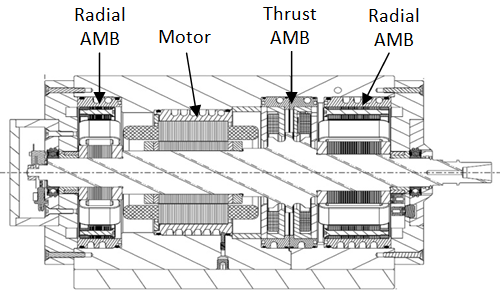
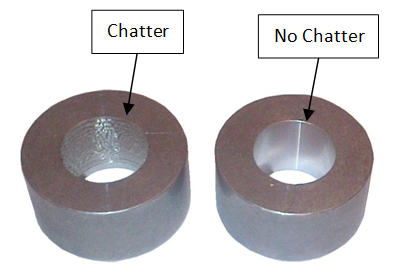
- Sawicki, J.T. and Pesch, A.H., “Experimentally Based Prediction of Machining Chatter Characteristics for AMB Spindle,” The 1st Brazilian Workshop on Magnetic Bearings, October 25-26, 2013, Rio de Janeiro, Brazil.
- Pesch, A.H. and Sawicki, J.T., “Uncertainty Range Estimation for μ-Synthesis Control of AMB Spindle,” accepted for The 10th International Conference on Motion and Vibration Control (MOVIC 2010), Tokyo, Japan, August 17-20, 2010.