Gas Turbine Finger Seals Design
RoMaDyC » Areas of Research » Tribology and Lubrication
Seals are a critical part of any gas turbine. As gas moves through the multiple stages of the compressor, pressure grows higher and higher. The tendency of the working fluid is to flow from high to low pressure. Therefore, in spaces where there is no mechanical forcing, the gas tends to leak back. Leakage is the enemy of power and efficiency.
A major seam where leakage occurs is the joint between the rotor and static parts of the engine. Because there is a velocity differential, there is no way to rigidly seal the joint. Several types of mechanisms have been used to seal this interface such as brush seals, labyrinth seals, foil seals, etc.
Finger seals are a relatively new device in which a pad is held against the rotor by a flexible “finger.” The pressure under the pad from the leaking fluid maintains the minimum needed clearance between the pad and the rotor. The stress on the finger assures that no more than the minimum required clearance, and therefor leakage, occurs. Research is being conducted at RoMaDyC to optimize the geometry of the finger-pad combination under different operating conditions of the gas turbine. It is an interesting optimization due to the need to simultaneously solve the fluid-dynamics problem for pressure distributions and the flexible body problem for the finger deflection.

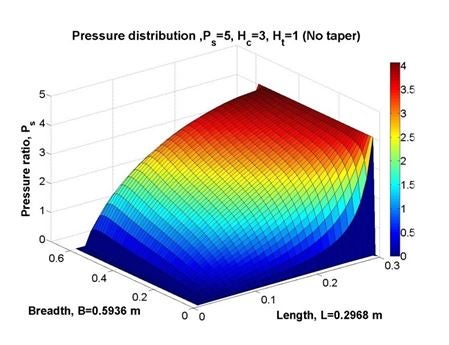
- Prabhat, G.P, Sawicki, J.T. and Fleming, D.P., “Analysis of Finger Seal Lift Pads,” ASME Paper GT2009-59842, ASME Turbo Expo 2009: Power for Land, Sea and Air, June 8-12, 2009, Orlando, FL, USA.