Model Updating of High-Speed AMB Machining Spindle Rotor
RoMaDyC » Areas of Research » Dynamics and Control
High-Speed Machining (HSM) spindles equipped with Active Magnetic Bearings (AMBs) are envisioned to be capable of autonomous self-identification and performance self-optimization for stable high-speed and high quality machining operation. The accuracy of the spindle rotor model in terms of physical and dynamic properties is essential to substantiate confidence in its predictive aptitude for subsequent analyses and robust MIMO controller generation.
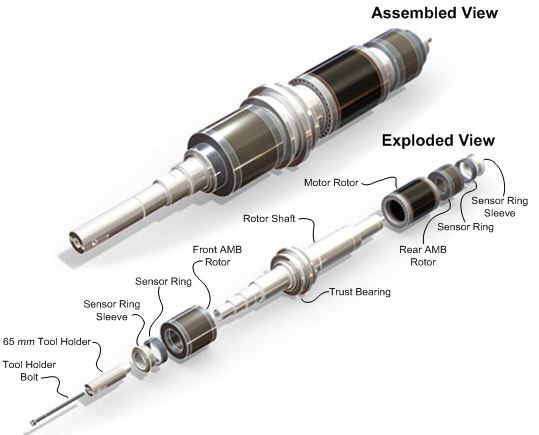
Dynamic modeling of complex structures is often a difficult task due to the many assumptions that are made throughout the modeling process. For example, the local stiffness contribution of the compression fit rotor components to the rotor’s global stiffness is not certain and contributes to the model’s inaccuracy. The amount of error between the experimental frequency response data and the finite element model can be easily observed by the errors of the resonance and anti-resonance peaks in the frequency response function.
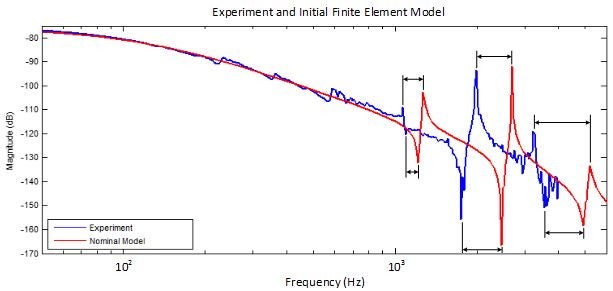
However, modeling error can be corrected through application of optimization routines to adjust model parameters in order to minimize error. Here, the rotor model’s adjustable parameters are the modulus of elasticity of carefully chosen finite elements. No other parameters were adjusted in order for all known features to remain intact such as dimensions, mass, center of mass, and polar and transverse moments of inertia. The objective function to minimize is the summation of all of the resonance and antiresonance peaks errors between the experimental data and the finite element rotor model. The final updated frequency response function of the rotor model matches the experimental data very well. As a result, this high-fidelity model can be used for predictive dynamics analyses as well as generation of MIMO robust controllers.

- Wroblewski, A.C., Pesch, A.H., and Sawicki, J.T., “Structural Change Quantification in Rotor Systems Based on Resonance and Antiresonance Frequencies Extracted from Frequency Response Functions,” Paper GT2013-95930, accepted for publication in ASME Journal of Engineering for Gas Turbines and Power, 2013.
- Wroblewski, A.C., Sawicki, J.T. and Pesch, A.H., “Rotor Model Updating And Validation for an Active Magnetic Bearing Based High-Speed Machining Spindle,” ASME Journal of Engineering for Gas Turbines and Power, 120136 (7 pages), 2012.